Application
Ferromagnetic metal contaminants – such as pieces of iron, steel and stainless steel – can enter your process in two ways: via the incoming product, or as a result of wear in the production process.
Goudsmit Cleanflow magnetic separators (drawer magnets) filter metal contaminants as small as 30 microns from powders and granulates in free-fall pipes. Applications are found in the plastics, food products, pharmaceutical and ceramic industries, among others.
Can stainless steel contaminants be filtered magnetically?’ Yes, they can! The material structure of stainless steel wear particles changes following plastic deformation. This makes them slightly ferromagnetic, making it possible to use of powerful magnets to filter them out of your product stream.
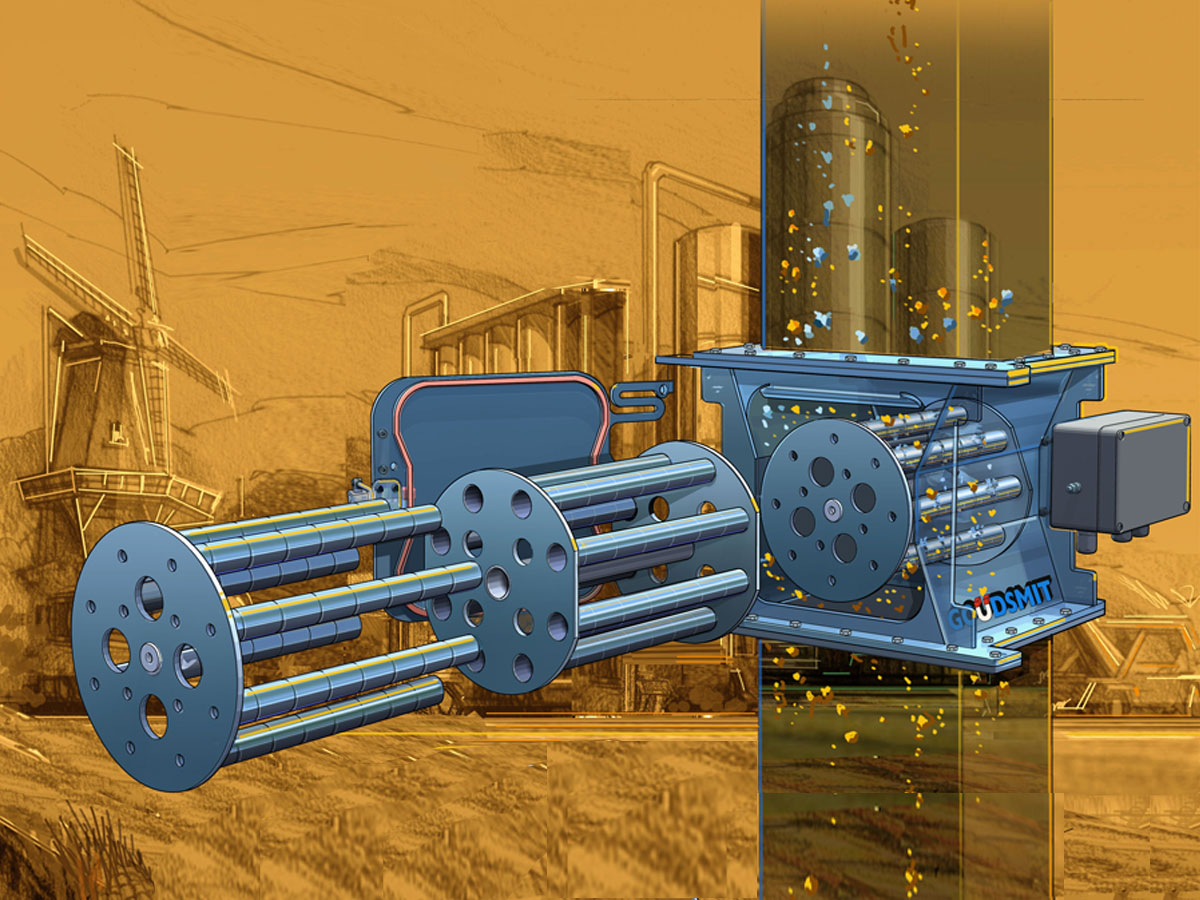
A metal detector cannot recognize very fine iron and stainless steel contaminants, but they can be captured by very strong magnets!
Working principle
The Cleanflow magnetic separators are built with very powerful neodymium magnetic bars. Because the bars are mounted in the middle of the free-fall pipeline, they are located in the centre of the product stream. This ensures that the product always passes very close to one or more magnets.
It is important to select a Cleanflow magnet housing that is one pipe size larger than the pipeline to maintain optimal product flow.
Types and placement of magnetic bars
Static
Static Cleanflow magnetic separators / drawer magnets are suitable for free-flowing products.
They have one row of thick magnetic bars, or two rows of thin ones, staggered one above the other.
If the magnetic separator is built with one row of thick bars, we install ’deflectors’ above the magnets when necessary, to ensure that the product always contacts or passes close to one or more bars.
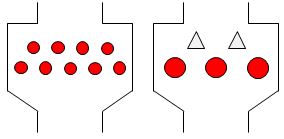
Rotating
Rotating Cleanflow magnets / drawer magnets are suitable for products that flow poorly – because they are sticky or greasy, for example – as a result of which bridging and accumulation may occur.
By rotating the magnetic bars the product continuously falls off of the bars. This keeps the bars cleaner, allows them to capture iron more effectively, and ensures that the product channel does not become blocked.
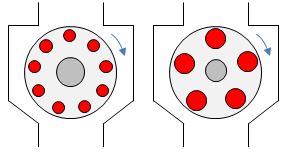
Products
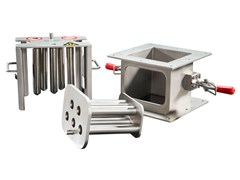
Cleanflows manual cleaning – Static
For magnetic filtration of small quantities of metal contamination from dry, free-flowing powders and granulates in non-pressurized pipes. Manual cleaning (quick cleaning).
Characteristics
- 2 magnetic grids, one above the other
- Manual quick cleaning
- Capacity 3 – 60 m³/h
- Types basic/food
- ATEX II 1/2 D
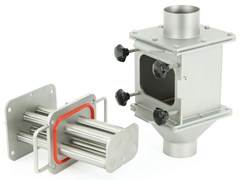
Pressure-tight Cleanflows manual cleaning – Static
For magnetic filtration of small quantities of metal contamination from dry, free-flowing powders and granulates in pipelines with a pressure of up to 1.5 bar. Manual cleaning (quick cleaning).
Characteristics
- 2 magnetic grids, one above the other
- Manual quick cleaning
- Capacity 2 – 30 m³/h
- Pressure-tight to 1.5 bar
- Atex II 1/2 D
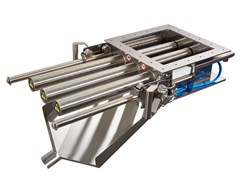
Cleanflows semi-automatic cleaning – Static
For magnetic filtration of small quantities of metal contamination from dry, free-flowing powders and granulates in non-pressurized pipes. Semi-automatic cleaning (Easy-clean).
Characteristics
- 1 Row of Ø50 mm bars
- Semi-automatic cleaning
- Capacity 3 – 80 m³/h
- Pressure-tight to 2 bar
- ATEX II -/2 D
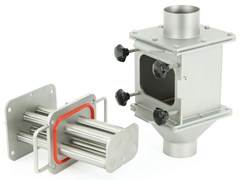
Cleanflows automatic discontinuously cleaning – Static
Suitable for use in applications with large quantities of metal contamination and where operator access is impossible. For dry, free-flowing powders and granulates. Automatic cleaning, with production stop.
Characteristics
- 2 magnetic grids, one above the other
- Automatic cleaning, discontinuous
- Capacity 30 – 90 m³/h
- Pneumatic or PLC control
- ATEX II 1/2 D possible
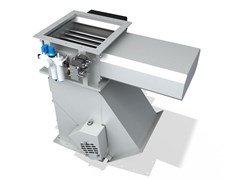
Cleanflows automatic discontinuously cleaning – Dust-proof – Static
Suitable for use in applications with large quantities of metal contamination and where operator access is impossible. For dry, free-flowing, dusty powders and granulates. Automatic cleaning, with production stop.
Characteristics
- 2 magnetic grids, one above the other
- Automatic cleaning, discontinuous
- Capacity 30 – 90 m³/h
- Dust-proof
- ATEX II 1/2 D
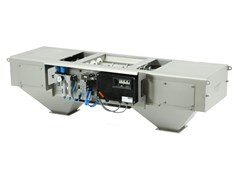
Cleanflows automatic continuously cleaning – Static
Suitable for use in applications with large quantities of metal contamination and where operator access is impossible. For dry, free-flowing powders and granulates. Automatic cleaning, without production stop.
Characteristics
- 2 magnetic grids, one above the other
- Automatic cleaning, continuous
- Capacity 30 – 90 m³/h
- ATEX II 1/2 D
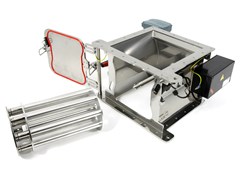
Cleanflows manual cleaning – Rotating
For magnetic filtration of small quantities of metal contamination from poorly flowing (e.g. fatty) powders in non-pressurized pipes. Manual cleaning (quick cleaning).
Characteristics
- 1 or 2 rotors with magnetic bars
- Manual quick cleaning
- Capacity 9 – 45 m³/h
- Types basic/food/pharma
- ATEX II 1/2 D possible
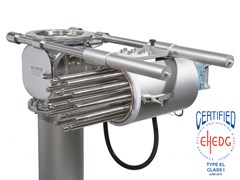
Cleanflows semi-automatic cleaning – Rotating
For magnetic filtration of small quantities of metal contamination from poorly flowing (e.g. fatty) powders in non-pressurized pipes. EHEDG certified. Semi-automatic
Characteristics
- Rotor with magnetic bars
- Semi-automatic cleaning
- Max. capacity 24 m³/h
- Hydroformed housing
- Atex II 1/3 GD
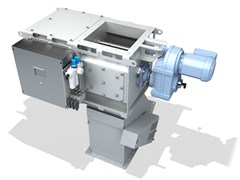
Cleanflows automatic discontinuously cleaning – Dust-proof – Rotating
Suitable for use in applications with large quantities of metal contamination and where operator access is impossible. For poorly flowing (e.g. fatty) powders and granulates. Automatic cleaning, with production stop.
Characteristics
- Rotor with magnetic bars
- Automatic cleaning, discontinuous
- Max. capacity 40 – 60 m³/h
- Dust-proof
- ATEX II 3D
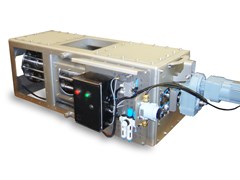
Cleanflows automatic continuously cleaning – Rotating
Suitable for use in applications with large quantities of metal contamination and where operator access is impossible. For poorly flowing (e.g. fatty) powders and granulates. Automatic cleaning, without production stop.
Characteristics
- Rotor with magnetic bars
- Automatic cleaning, continuous
- Max. capacity 40 – 60 m³/h
- Dust-proof
- ATEX II 3D possible
Bar cleaning: manual, semi-automatic or automatic
Manual ’quick cleaning’
Magnetic bars are enclosed in extractor tubes which eliminate the need for manual wiping. This makes cleaning simpler, and we call it ’quick cleaning’. By pulling the magnetic bars out of the extractor tubes, the captured metal contamination falls off the bars itself.
In this arrangement the extractor tubes also serve to protect the magnetic bars, so they wear less and therefore last longer.
Semi-automatic cleaning (’Easy-Clean’)
The magnet unit can be pulled out of the housing manually – over a side guide – after which the magnets in the enclosing tubes automatically slide out a step further. As a result, the iron automatically falls off the enclosing tubes.
Semi-automatic cleaning is simpler and requires less effort from the operator than manual quick cleaning, because the magnet unit does not have to be removed, lifted and moved. An additional, major advantage is that the magnets and tubes suffer less wear and potential damage.
Automatic cleaning
An electric start signal controls a fully automatic cleaning cycle. This signal can be given on the machine or from a control room.
- Automatic discontinuous cleaning: for these types the product flow must be stopped to perform a cleaning cycle.
- Automatic continuous cleaning: for these types the cleaning cycle can simply be performed during production.